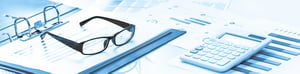
Return on Investment Calculator ➖
Estimate How Much Money You Can Save Annually With Solvent Recycling
Complete the fields below and click “Calculate” for each solvent recycled in your facility to estimate your solvent purchase and disposal costs savings over time with solvent recycling.
Estimated Annual Savings with Recycling |
*This calculation is approximate and based on user input – results should be considered an estimate.