Smarter Solvent Recovery for Dental Labs Using Additive Manufacturing
SolvTrue™ Solvent Recycling System Delivers High-Concentration IPA, Lower Costs, Proven Results
For dental labs using additive manufacturing, clean parts aren't just important—they're critical to patient safety and product performance. As 3D printing becomes the standard for producing custom dental fixtures, it brings with it an increased reliance on solvents like Isopropyl alcohol (IPA) to clean printed components.
One leading dental lab found that their IPA usage was climbing fast—along with the associated costs and chemical waste. Their team needed a way to maintain high production standards while reducing waste, lowering costs, and supporting a more sustainable workflow. That’s when they partnered with CBG Biotech to evaluate the SolvTrue™ S700 solvent recovery system.
The lab's objectives were clear:
- Reclaim high-concentration IPA suitable for reuse
- Cut solvent purchasing costs
- Maintain consistent cleaning quality for resin-printed parts
- Reduce hazardous waste and improve sustainability
Test Setup
CBG Biotech conducted a controlled test using the SolvTrue™ S700V system, which is engineered for reclaiming solvents like IPA from resin-based waste streams.
Materials and Equipment Included:
- Used IPA from the lab’s cleaning process
- Waste materials: Luticone Digital Print™ 3D Denture Resin, Sprintray Apex Base, and Sprintray Apex Teeth
- SolvTrue™ S700V distillation unit (220V)
- Tank liner (PP7) for easy waste removal
- Mist deflector (DF1000) to prevent contamination during boil
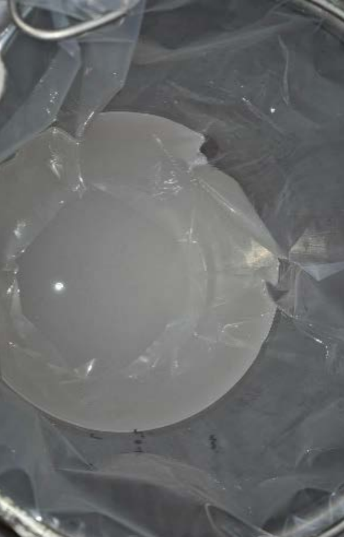
Figure 1: Waste IPA sample before processing
Standard IPA recovery parameters were used, including a jacket temperature offset of 30°C, an underboil offset of 40°C, and a 10-minute delay before boiling. These settings are designed to gently and efficiently distill IPA from complex resin-based mixtures without degrading solvent quality.
Results at a Glance
The system completed the distillation cycle in 5.36 hours and automatically shut down once the IPA vapor production decreased. After the unit cooled, the recovered IPA and remaining residue were collected and analyzed.
- Initial mixture mass: 27.6 lb
- Recovered IPA: 25.8 lb
- Waste residue: 1.02 lb
- Recovered IPA yield: 97% of net mass
- Recovery rate: 0.73 gallons per hour
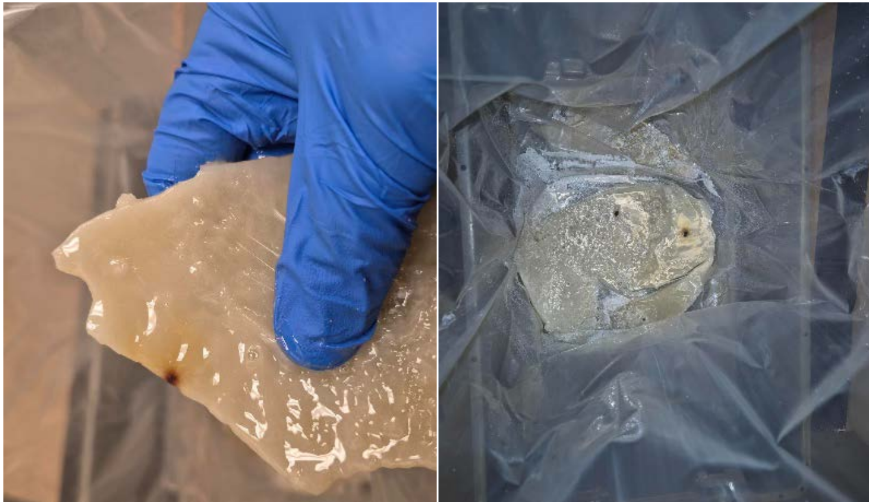
Figure 2: Post-distillation tank residue
The resin residue left behind appeared mostly cured, with little remaining solvent—making disposal easier and safer. The IPA recovered was clear and free from visible contaminants.
Figure 3: Recovered IPA sample
Concentration Testing & Quality Validation
Ensuring the quality of the recovered IPA was a top priority. A sample of the reclaimed solvent underwent concentration testing using an alcohol hydrometer, along with tools such as a scale, pipette, and beaker to confirm specific gravity.
The initial hydrometer reading was approximately 101%. Applying a temperature correction factor of 3% yielded an estimated IPA concentration of 99%. Additional testing showed a specific gravity of 0.779 g/mL—closely aligned with the benchmark of 0.781 g/mL for 100% IPA at 25°C.
Figure 4: Hydrometer reading of recovered IPA Figure 5: Specific gravity test results
These readings confirmed that the recovered IPA maintained a high level of concentration—suitable for reintroduction into the lab’s cleaning process without risk to product quality or consistency.
Conclusion
The SolvTrue™ S700V successfully reclaimed more than 95% of the IPA used in this dental lab’s cleaning process, producing a solvent with a high-concentration level that met the lab’s strict quality standards. By implementing an on-site recovery solution, the lab was able to significantly reduce their solvent spend, cut down on hazardous waste, and support their ongoing commitment to sustainable operations.
The test achieved the following key outcomes:
- Recovered IPA was clean and fully suitable for reuse
- Overall IPA consumption and costs were reduced
- Solvent concentration supported reliable and effective parts cleaning
- Sustainable recovery process reduced chemical waste
The dental lab now has a proven, cost-effective way to manage IPA use without compromising quality—while gaining greater control over their operations and environmental impact.
Download the Full Case Study
Want full results, data, and testing details? View and download the complete case study PDF.
Questions?
If you have questions about this report or want to discuss its findings, reach out to CBG Biotech. Our team can help determine if a recycling solution is the right fit for your operations.