Subscribe to our Blog
Virtually every part that's manufactured needs to be washed before it's ready for use, whether it's a plastic part for a toy or a precise metal part used in an aircraft. During the manufacturing process, some combination of cutting oil, grease and grime is introduced, and removing any of these substances is ultimately required to pass quality-control checks and, most importantly, ensure public safety.
One of the most common ways to effectively wash parts is with cleaning solvents.
Consistently Clean Parts Save Manufacturers Time and Money
While public safety and the proper operation of equipment are paramount, establishing a process that ensures consistently clean industrial parts also benefits manufacturers in a number of ways.
Parts that fail quality control cleanliness checks can potentially contaminate properly cleaned parts, especially if two or more components are used in a combined part. Worse, those improperly cleaned parts will need to be rerun or completely scrapped. All of this negatively impacts production output, lead times and, eventually, the bottom line.
The Role of Industrial Parts Washing Systems
There are two primary types of industrial parts washing systems, standard immersion-types and vapor degreasers.
Immersion-type parts washers come in many configurations, but their primary function is the same—they introduce parts to cleaning solvents via immersion. Some immersion-types also come with added features like agitators that jostle parts for deeper cleaning.
Conversely, vapor degreasers are completely different types of machines and used for precision parts cleaning. They vaporize solvents by heating them, which allows the solvents to p
The Role of Solvents
More often than not, manufacturers who use immersion-type parts washing equipment are using a cleaning solvent like mineral spirits, or a naphtha-based liquid hydrocarbon compound, all of which are some form of petroleum distillate.
These types of parts cleaning solvents are extremely common, and not without their limitations. First, they can only be used in immersion parts washing and should never be used in degreasing processes as they're highly flammable. There are also many types of mineral spirits available on the market. This means that determining their effectiveness is specific to application requirements—and different materials—and is often done through trial and error.
However, these solvents are perfect in applications where white-glove precision is not required, and large quantities of extremely dirty parts need to be cleaned.
Vapor degreasing operations often use any number of common fluorinated solvents, such as Vertrel™ or Novec™. These highly stable, nonflammable, sustainable solvents can be reused many times (with the help of trusted solvent distillation equipment) and not lose their efficacy. Fluorinated solvents are also compatible with a wide variety of materials and are highly efficient; they evaporate quickly and leave little residue.
Some of the hazardous solvents still used in vapor degreasing applications include trichloroethylene, perchloroethylene and n-propyl bromide (nPB), although their usage has declined based on the availability of safer alternatives over the last 20 years.
Fluorinated solvents and isopropyl alcohol are also increasingly playing larger roles in innovative production processes like stereolithography (SLA), an additive manufacturing process, or 3D printing technology, used to create prototypes and models of parts prior to production. Solvents are being used to both cure objects created using this process and clean the final products. Because the final product is always a plastic composite, a standard immersion-type parts washing process is used for cleaning, as opposed to a vapor degreasing process.
The Case for Solvent Distillation Equipment in Parts Cleaning Processes
Solvent distillation equipment fits into the larger trend of manufacturers making processes and operations safer, automated, cost-effective and sustainable.
Safety: Each solvent distillation unit is a closed-loop system that ensures workers don't come into contact with solvents. |
Automation: Solvent distillation equipment can be fully integrated into parts washing systems, expediting processes and saving labor hours. Even units that aren't integrated require minimal attention from workers. |
Economics: In addition to saving labor hours tied to solvent waste disposal and handling, units can reduce solvent purchases by up to 90%. |
Sustainability: When you recycle solvents, your entire industrial operation produces far less hazardous waste and is more environmentally friendly. |
Learn More
For these reasons, ranging from strategic to tactical, it’s important to evaluate the security of your supply chain for organic solvents with the use of our production recyclers. CBG Biotech's industrial business development executives stand ready to meet your needs for recovering your own organic solvents with SolvTrue™ production recyclers. If you have a question or would like more info, please call 800-941-9484 (and press option 3 for support) or get in touch with us online today!
Check out these other helpful resources:
- Blog Post: Recycling IPA for 3D Printing with SolvTrue™
The benefits of using SolvTrue™ Solvent Recyclers to recover industrial organic solvents in order to increase production capacity. - Video: How to Use SolvTrue™ PW4 Solvent Recycler
SolvTrue™ industrial solvent recyclers improve operational and production processes by reducing solvent waste and disposal costs and allowing you to maintain an efficient and sustainable operation without compromising quality or safety. - Video: Features of the SolvTrue™ S700
SolvTrue™ industrial solvent recyclers improve operational and production processes by reducing solvent waste and disposal costs and allowing you to maintain an efficient and sustainable operation without compromising quality or safety.
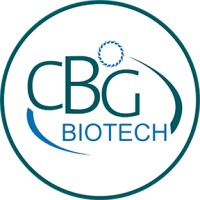
COMMENTS